Q: I burned an old Fisher airtight stove for many years. The Fisher had a HUGE firebox (I'm guessing 4 cu.ft. or more), and had spin-draft
controls you could close all the way if you wanted to. With the big load and the spin-draft controls, I had no problem "holding" the fire overnight.
Two years ago I gave in to my neighbors' complaints about my smokey chimney and switched to an EPA approved model with a 3.2 cu.ft. firebox
(size large for today's super-efficient stoves). I was hoping to get a longer overnight burn, and just the opposite happened. The new stove does put
out more heat than the Fisher did (even though it is smaller), but it won't hold the coals as long, even when I turn the draft control down all the
way! I called my dealer and he said I should blame the EPA. Can you explain?
Puzzled in Pittsburgh
First, a little background info:
An Ideal burn cycle should heat the load of fuelwood to gasification temperature (Stage 1), burn the volatile gases to extract their heat value and
clean up the exhaust (Stage 2), then maximize the duration of the fire as the wood fiber burns down to its final, charcoaling phase (Stage 3).
The most oxygen-hungry of the three phases of a wood fire is Stage 2, when the temperature of the load approaches 500° and the wood resins
begin to gasify. With a big load in a size-large firebox, the "bloom" of volatile gases that floods the firebox during Stage 2 can be considerable, and
a correspondingly sizeable quantity of oxygen is needed to burn it and extract its heat value.
Why your old Fisher could go so long between refuelings:
The old spin-draft airtights like your Fisher enabled the operator to prolong the duration of each burn by starving the fire for air. During those low,
smoldering fires there wasn't enough oxygen in the firebox to consume the Stage-2 bloom of volatile gases, so they escaped up the flue, taking as
much as half of the heat value of that load of wood along with them. And lost heat wasn't the only bad news: smoldering also causes excessive
creosote formation in the flue, and (as you mention) provokes complaints from smoked-out neighbors.
1988: Complaints from smoked-out neighbors get the EPA involved:
To help clean up the airshed, EPA emissions regulations require that new wood stoves consume the gasified wood resins. This is accomplished
through a process called secondary combustion, wherein a second fire inside the firebox reburns the exhaust from the primary fire.
The problem with maintaining secondary combustion in big fireboxes:
When a BIG load reaches Stage 2, the "minimum" airflow required for secondary combustion can be substantial. Providing enough airflow to meet
EPA low-emissions standards during Stage 2 of the burn presents a major engineering challenge to designers of size-large wood stoves. The most
popuiar solution seems to be the incorporation of a "stop" in the design of the draft control, so it can't be closed down below a certain point. While
this method might get a stove through EPA testing, there's a big downside: with no "low" draft control setting available, an abundance of
combustion air is delivered to the fire even when it isn't needed, causing faster than necessary fuel consumption during the other stages of the fire.
This results in frustrated owners of size-large stoves who find they can't "hold" the fire as long as they might want to between refuelings.
Pacific Energy's patented solution:
When designing the size-large Neo 2.5,
Neo 2.5 Insert, Summit, Summit Classic, Alderlea T6 and Summit Insert models, the engineers at Pacific Energy incorporated
several of the same techniques used in their smaller models to extend the duration of each burn, including continuous-bead welded fireboxes and
tight fitting loading doors to minimize unwanted air infiltration into the fire. Mindful of consumer complaints about the lack of low-end control built
into many of today's larger stoves, they also introduced the patented Extended Burn Technology (EBT) device, which delivers a burst of extra air
to the fire only as needed to maintain secondary combustion during Stage 2 of the fire.
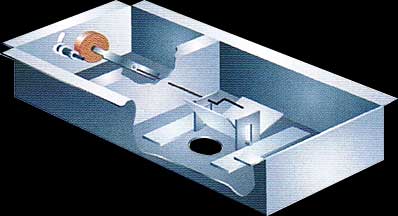
1998: PE's Patented "Series A" EBT Mechanism
| |
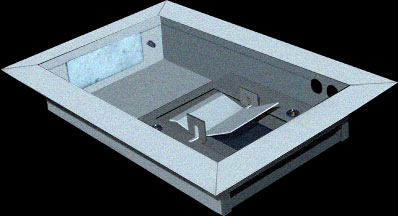
2013: PE's Patented "Series B" EBT Mechanism
|
The original Extended Burn Technology device incorporates a pivot
plate, mounted so its base covers a "boost air" intake opening. The plate
is pivoted by an actuator arm attached to a bimetallic coil, which turns
the arm in response to rising firebox temperatures when the volatile
gases ignite at the beginning of Stage 2 of the burn. As the coil heats up,
the plate hinges open to uncover the intake opening and provide extra air
to the fire. When the gases have been consumed and the firebox
temperature returns to normal, the coil contracts, lowering the base plate
back down to seal the opening and stop the extra airflow. | | The Series B device is driven by a predictable increase in chimney
updraft at the beginning of Stage 2 due to the rise in exhaust
temperature when the gasified resins ignite. The increased updraft
draws a balanced pivot plate open, uncovering an intake opening to
provide the "boost air" needed to ensure complete combustion of the
volatile gases. Unlike the original EBT device, which delivers the boost
air to the primary fire, the new device feeds the extra air to the
secondary flames only. The operator retains control of the burn rate of
the primary fire, and longer burn times are easier to achieve. |
To sum up:
When a wood stove is equipped with either version of Pacific Energy's Extended Burn Technology, neither the manufacturer nor the
operator has to worry that the manual draft control might be set too low to supply sufficient air to achieve the cleanest, most efficient burn. Should
a situation arise where the oxygen supply becomes insufficient to consume the "bloom" of volatile gases produced during Stage 2 of the burn, the
mechanism automatically provides the extra air needed for complete combustion. This enables the stove to be operated at a truly "long burn"
setting without fear of lost heat value, excessive creosote formation or smoked-out neighbors.
To return to the page you came from, use the < BACK button on your browser or click a button below:
<
|